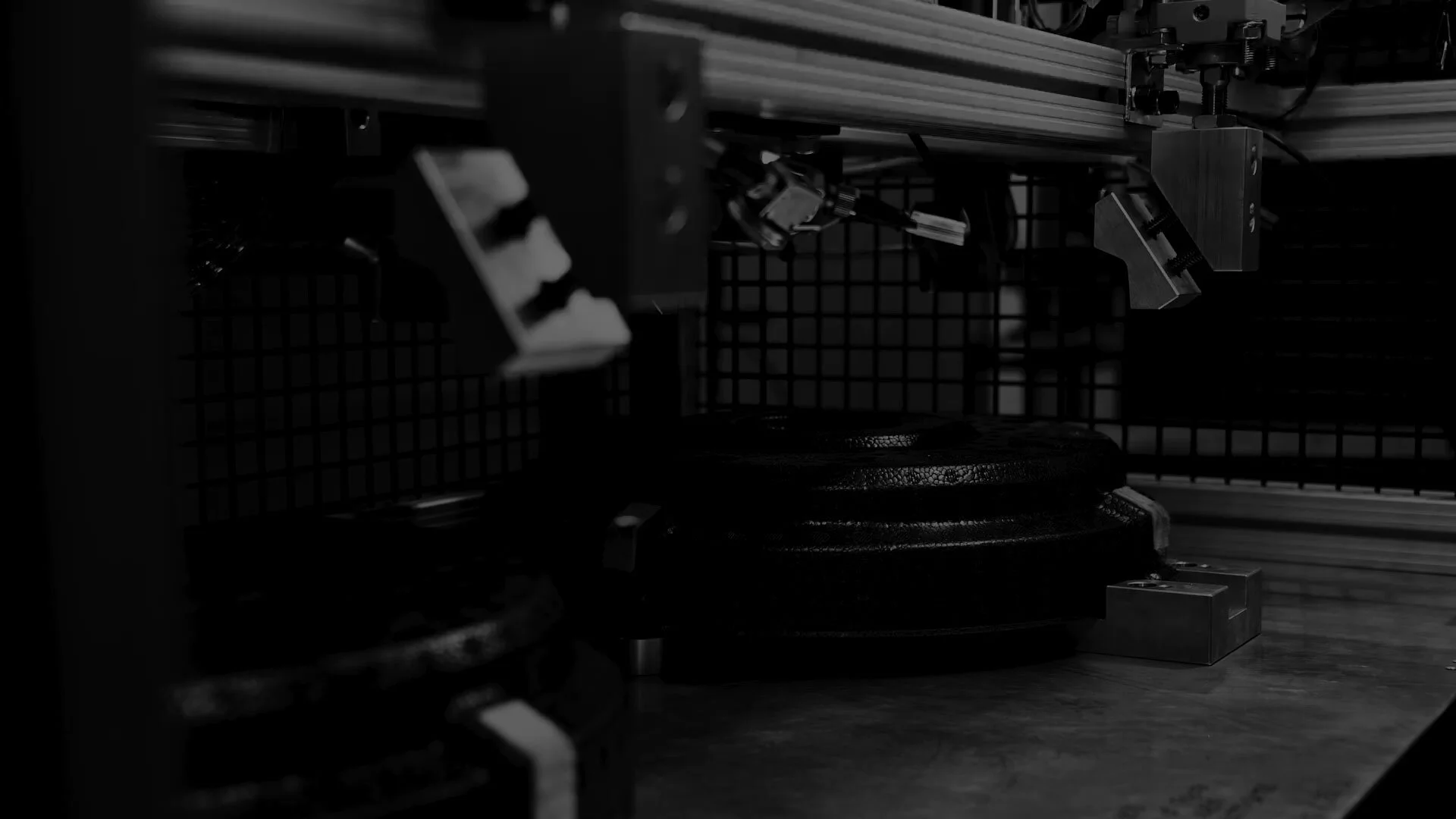
AUTOMATION
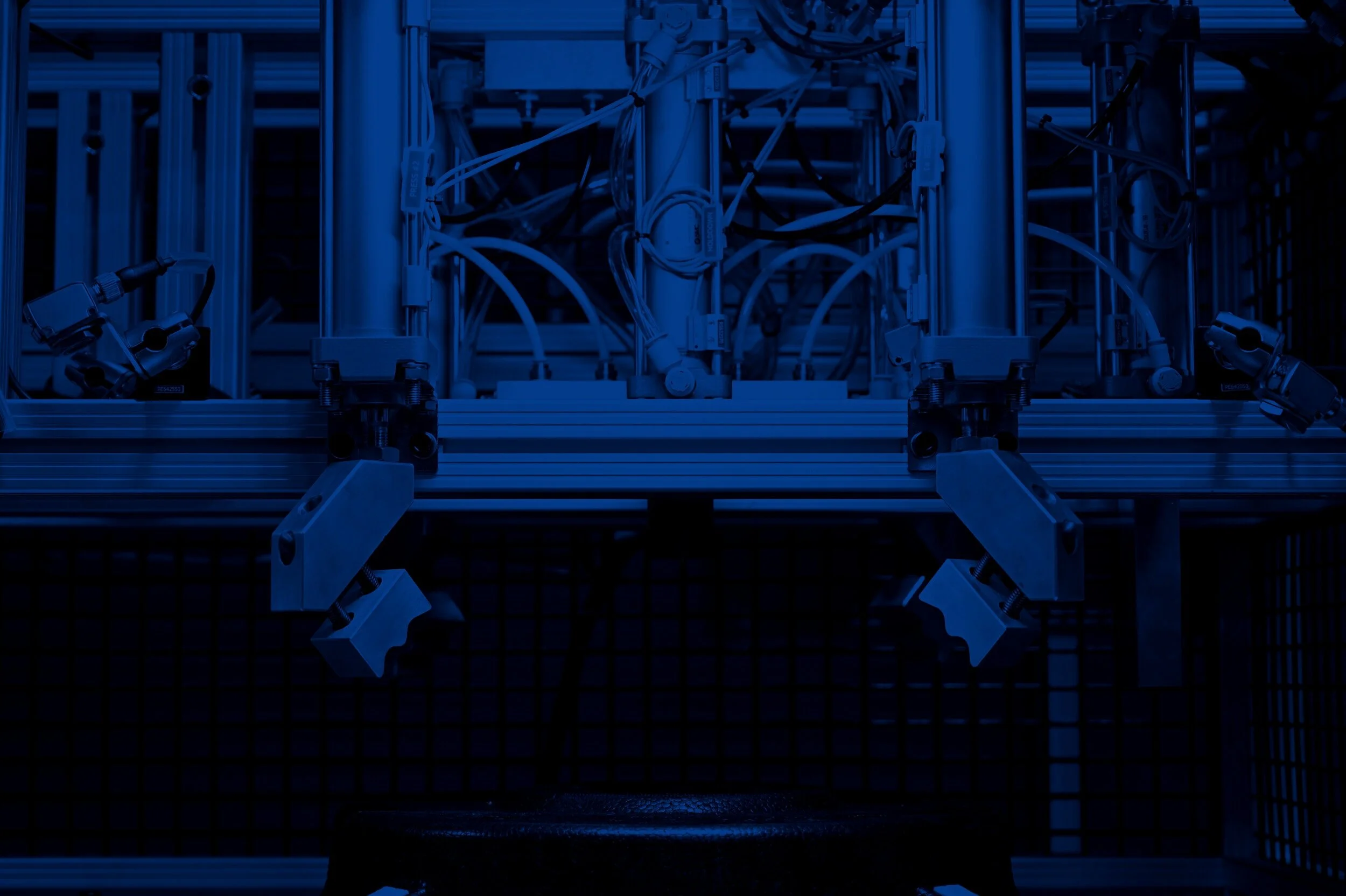
When precision matters most, you can trust APT.
APT relies upon our seasoned engineering staff to comprehend customer requirements for numerous industries. We are committed to providing high-quality, low maintenance automation solutions. We take pride in implementing systems with future-friendly designs to enable maximized efficiency.
Our specialized background includes the development of:
Poka Yoke stations
Vision-controlled equipment
Robotic cells for automated welding, cutting, assembling, or inspecting
Stand-alone workstations for edgewrapping of soft-trim
* NDA agreement will enable APT to provide details
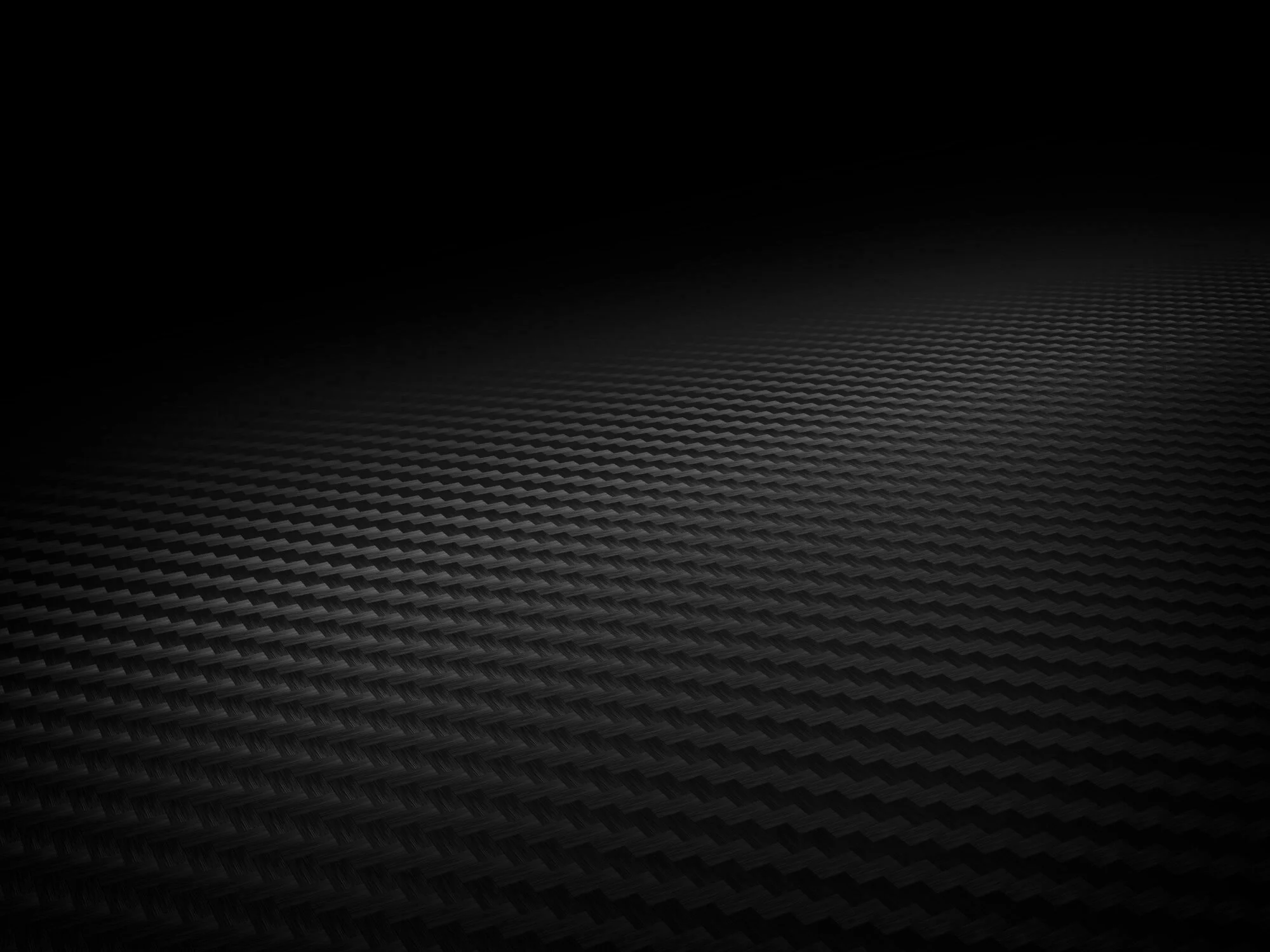
AUTOMATION SOLUTIONS
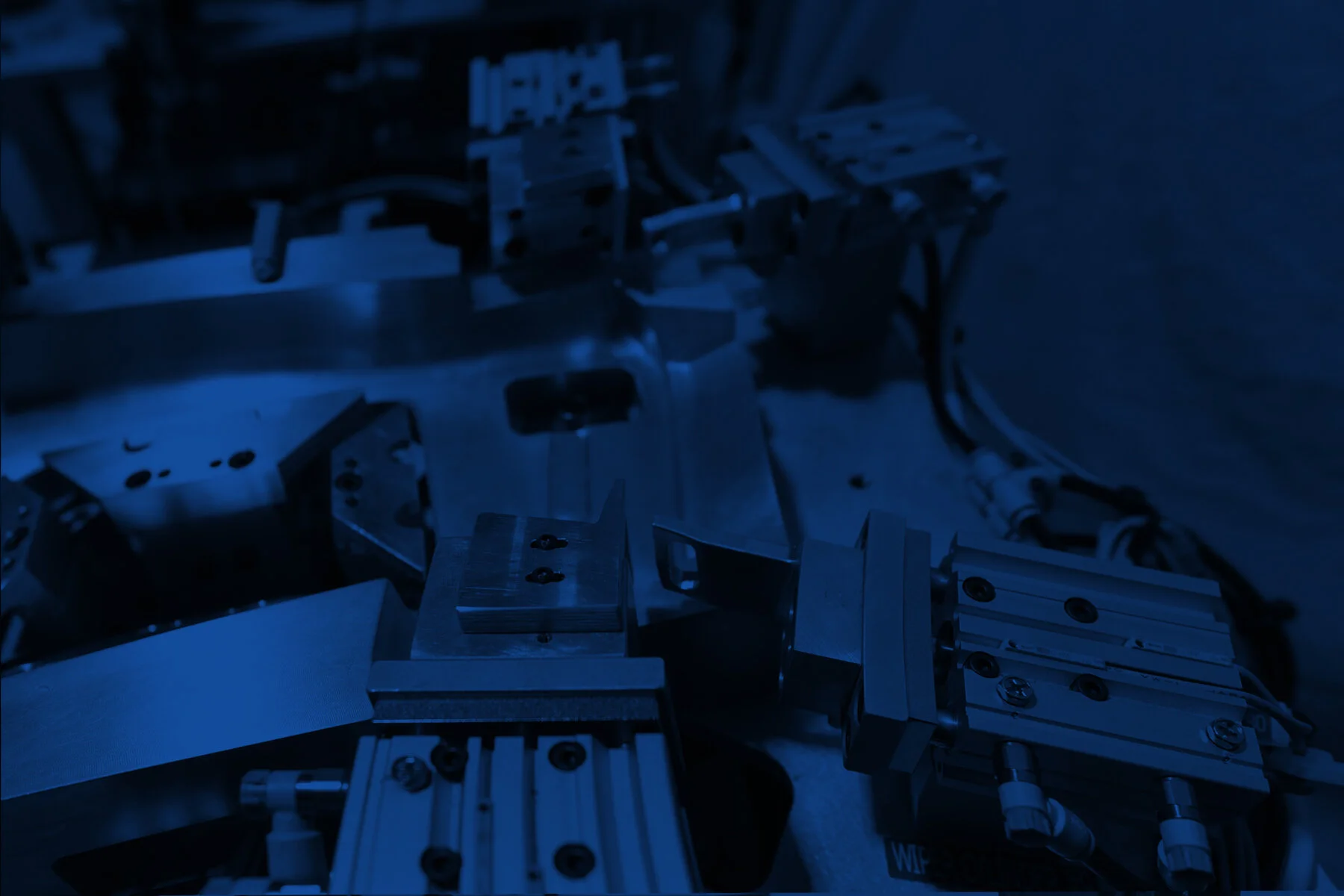
Specialty Tooling
Our in-house manufacturing capabilities allow us to take on custom specialty tooling projects for our customers. Our design team can help develop your vision into a fully detailed design that our manufacturing technology centre (MTC) can manufacture. Dies, lamination equipment, or other specialty tooling (large or small) can be developed, tested, and proven at our facility before being delivered to you.